5 Essential Steps to Do and Polish Ironstone Matrix Opal
Polishing ironstone matrix opal involves meticulous methods and the right tools. Start by shaping with coarse grit sandpaper and progressively finer grits.
Use diamond pastes and cerium oxide for polishing; both deliver ideal outcomes. Employ a felt wheel or leather lap for an even sheen, and optimize you use a slow, steady motion with light pressure.
Maintain the opal’s shine by cleaning regularly with a soft cloth and avoiding abrasive materials. Periodically, apply a commercial opal conditioner.
Store the opal in a dry place and avoid harsh chemicals or extreme temperatures for longevity. Master these techniques for perfect results.
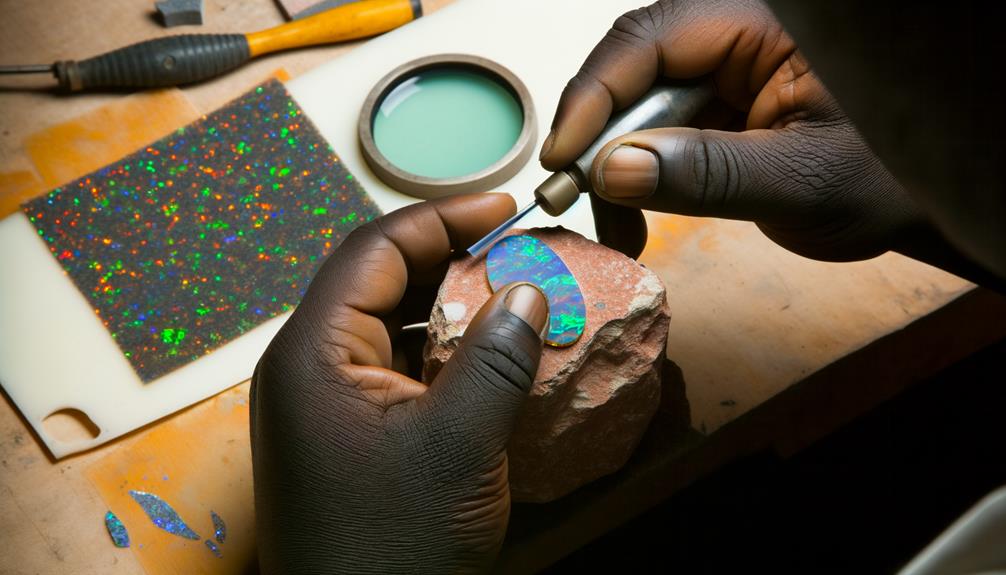
Key Takeaways
- Start by shaping the opal with a coarse grit sandpaper, then progressively use finer grits for smoothing.
- Use diamond pastes or cerium oxide for the final polishing stage to achieve a high shine.
- Employ a felt wheel or leather lap for polishing, using slow, steady motions and minimal pressure.
- Keep the opal cool and clean during the process by maintaining a constant water flow and regularly wiping with a soft cloth.
- Avoid using abrasive materials and harsh chemicals, and periodically apply an opal conditioner to maintain the polish.
Understanding Ironstone Matrix Opal
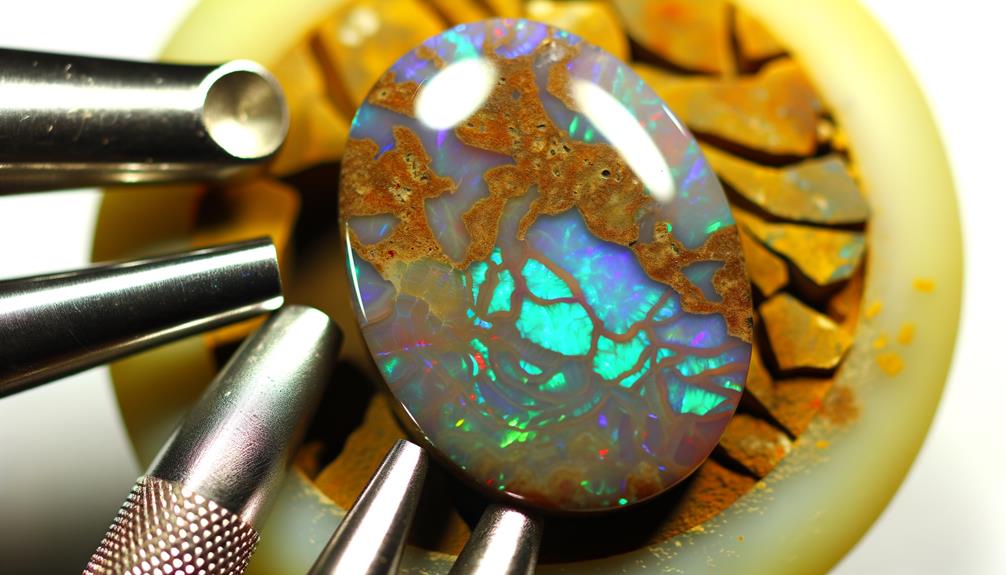
When delving into ironstone matrix opal, it’s necessary to recognize that this unique gemstone is characterized by opal deposits interspersed within a host rock of ironstone.
The ironstone provides a contrasting background, accentuating the opal’s vibrant play-of-color.
You’ll find that the matrix can vary in hardness, which influences the polishing process.
Opal content within the matrix affects the overall appearance and value.
To achieve best results, understand the specific characteristics of your specimen.
Assess the proportion of opal to ironstone, noting that higher opal concentrations typically yield more striking visual effects.
Grasping these nuances is essential for effective polishing, ensuring you enhance the gemstone’s natural beauty without compromising its structural integrity.
Choosing the Right Tools
To achieve a high-quality finish on ironstone matrix opal, you must select the appropriate grit sandpaper, best polishing compound, and suitable buffing tools.
Start with coarse grit sandpaper to shape the stone, then progressively use finer grits to smooth the surface.
Selecting Grit Sandpaper
Selecting the appropriate grit sandpaper is crucial for achieving a smooth and polished finish on ironstone matrix opal. You need to understand the progression of grit sizes, starting with coarse and advancing to fine. Begin with a 220-grit sandpaper to remove surface imperfections and shape the opal. Progress to 400-grit to refine the surface and eliminate deeper scratches. Use 600-grit for finer smoothing, and finish with 1200-grit for a pre-polish.
Grit Size | Purpose |
---|---|
220 | Initial shaping, rough removal |
400 | Refining, eliminating deep scratches |
600 | Fine smoothing |
1200 | Pre-polish, final preparation |
This systematic approach guarantees that each stage builds upon the last, resulting in a flawless, polished opal.
Optimal Polishing Compound
After progressing through the grit sizes, you must now focus on selecting the best polishing compound to achieve the desired luster on your ironstone matrix opal.
Opt for diamond pastes in the micron range, ideally between 1 to 3 microns, for best results. Diamond’s hardness will effectively polish the opal without causing unnecessary abrasion.
Cerium oxide is another excellent choice; it provides a fine polish and enhances the stone’s natural fire. Make sure that your polishing compound is specifically designed for precious stones to avoid any potential damage.
Applying the compound evenly and consistently is essential for achieving an ideal finish. Always test a small area first to gauge the compound’s effectiveness and adjust your technique as needed.
Appropriate Buffing Tools
When polishing ironstone matrix opal, using the correct buffing tools is vital for achieving a high-quality finish without harming the stone. You must choose tools suitable for the hardness and texture of the opal. Diamond-infused wheels, felt buffs, and muslin wheels each have a specific role in the polishing process. Here’s a useful guide to selecting the appropriate tools:
Tool Type | Purpose |
---|---|
Diamond Infused Wheel | Initial smoothing and shaping |
Felt Buff | Intermediate polishing, refining |
Muslin Wheel | Final high-gloss finish |
Leather Buff | Delicate final touch |
Hard Rubber Wheel | Precision edge work |
Proper tool selection guarantees you achieve a stunning, damage-free polish, highlighting the opal’s innate beauty.
Preparing Your Workspace
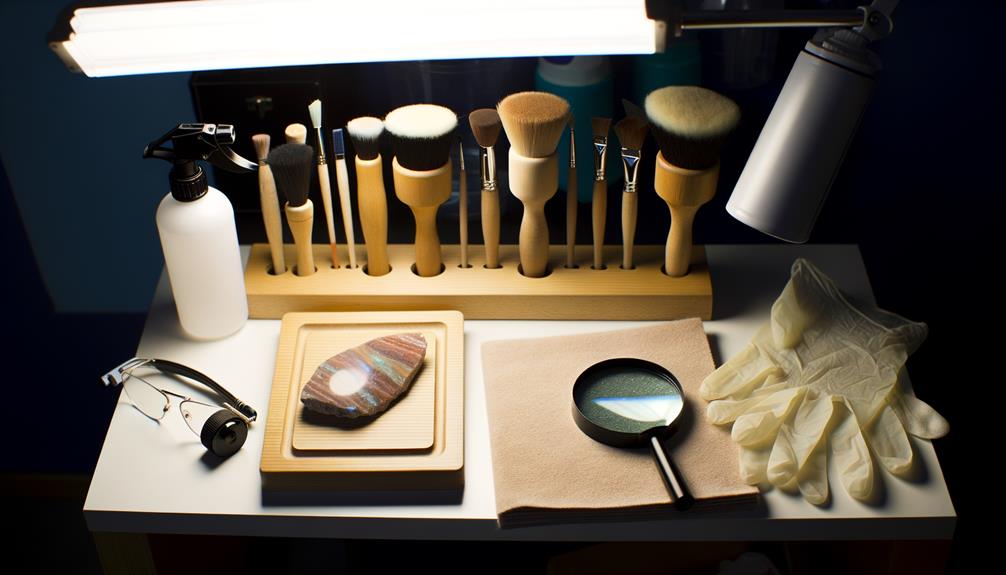
First, gather all necessary tools, including your polishing machine, water supply, and abrasives, to guarantee efficiency.
Guarantee proper lighting to meticulously observe the opal’s surface during polishing. Inadequate lighting can lead to imperfections and overlooked flaws.
Gather Necessary Tools
To prepare your workspace for polishing ironstone matrix opal, gather essential tools like a trim saw, diamond grinding wheels, and a polishing machine. These tools are critical for shaping, smoothing, and achieving a high-gloss finish on your opal. Make sure your trim saw is equipped with a fine blade to make precise cuts.
Diamond grinding wheels of various grits will allow you to systematically refine the opal’s surface. Finally, a reliable polishing machine with appropriate polishing compounds is necessary for the final touch.
Essential tools to gather:
- Trim saw: Fine blade for precision cutting.
- Diamond grinding wheels: Different grits for progressive smoothing.
- Polishing machine: Uses polishing compounds for a high-gloss finish.
Having these tools within reach ensures efficient, high-quality results.
Ensure Proper Lighting
With your tools ready, focus on ensuring proper lighting to meticulously see every detail of the ironstone matrix opal during the polishing process. Adequate lighting is essential for identifying imperfections and achieving a high-quality finish. Use a combination of overhead and task lighting to reduce shadows and enhance visibility. Opt for LED lights with a color temperature of 5000K to emulate natural daylight, ensuring accurate color representation.
Lighting Type | Features |
---|---|
Overhead | General illumination |
Task | Focused, adjustable light source |
LED | Energy-efficient, long-lasting |
5000K | Natural daylight simulation |
Position lights to eliminate glare and reflections. Regularly inspect the opal under different angles to catch inconsistencies. Proper lighting will significantly impact the final polish, revealing the opal’s true beauty.
Initial Shaping Techniques
Begin initial shaping of ironstone matrix opal by carefully grinding the rough stone with a diamond wheel to outline its basic form. Focus on maintaining control and precision to avoid over-grinding, which can damage the opal.
Determine the orientation: Identify the best face of the opal to maximize its color play and visual appeal.
Mark guidelines: Use a fine-tip marker to outline the desired shape and any areas to be preserved.
Monitor temperature: Continuously check the stone’s temperature to prevent overheating, which could cause fractures.
Carefully rotate and tilt the opal, ensuring an even grind across the surface. Consistency in pressure and motion is essential. These steps establish a foundational shape, setting the stage for more detailed refinement.
Sanding and Smoothing
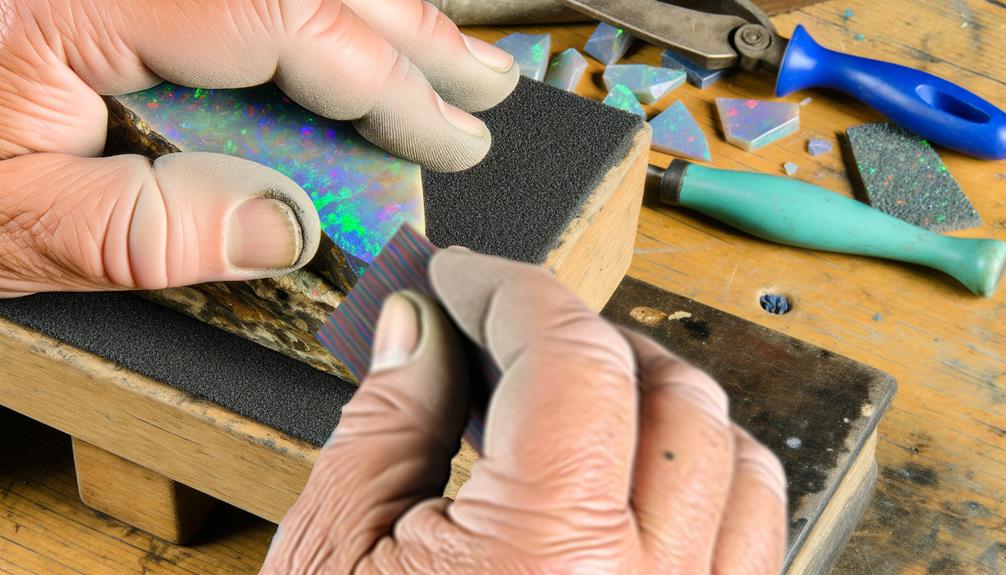
You should start polishing the ironstone matrix opal using progressively finer abrasives to achieve a smooth and even surface. Begin with a coarse grit, around 220, to eliminate any rough edges. Then, sequentially move to 400, 800, and 1200 abrasives, guaranteeing each shift eliminates scratches from the previous grit. Maintain a constant water flow to prevent overheating and remove debris.
Grit Level | Purpose |
---|---|
220 | Initial rough polishing |
400 | Intermediate smoothing |
800 | Fine polishing |
1200 | Pre-polishing refinement |
2000+ | Ultra-fine finishing |
Consistently check the opal’s surface for uniformity. This precise method ensures the matrix opal is adequately prepared for the polishing stage. Keep your workspace clean to observe the results clearly.
Polishing to Perfection
Achieving a mirror-like finish on your ironstone matrix opal demands meticulous attention to detail and the use of specialized polishing compounds. Start with a felt polishing wheel and apply a high-quality diamond paste. Work slowly, using light pressure to avoid overheating and damaging the opal. Adjust your technique based on the opal’s response, ensuring uniform coverage and avoiding flat spots.
Key considerations include:
- Polishing Compound Selection: Choose diamond paste or cerium oxide.
- Equipment: Use a felt wheel or leather lap for best results.
- Technique: Employ a slow, steady motion and minimal pressure.
Maintaining the Shine
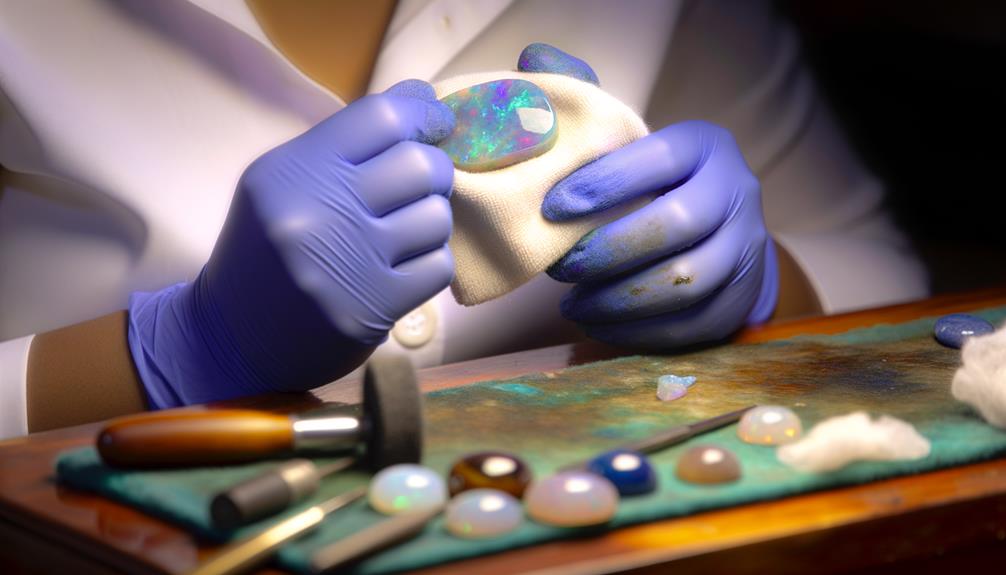
To maintain the opal’s dazzling shine, regularly clean the surface with a soft, lint-free cloth and inspect for any signs of wear or scratches.
Avoid using abrasive materials that could degrade the polish. If you notice minor scratches, gently buff the area with a fine polishing paste specifically designed for opals.
Keep the opal dry; excessive moisture can compromise its integrity. Store the opal in a padded, separate container to prevent contact with harder gemstones.
Periodically, reapply a commercial opal conditioner to restore luster. Avoid exposing the opal to harsh chemicals or extreme temperatures, as these can cause damage.
Conclusion
By meticulously following these steps, you’ll transform rough ironstone matrix opal into a beautifully polished gem. Remember, patience is critical.
For instance, when John followed this method, his opal’s brilliance exceeded expectations, showcasing vivid colors. Consistently use appropriate tools and techniques to maintain its shine.
Regularly inspect and clean the opal, ensuring it remains an enchanting piece. With careful attention, you’ll master the art of polishing ironstone matrix opal, achieving professional results.